Mechanically Latched Vacuum Contactors
Mechanically latched vacuum contactors do not require a continuous control power source. A short control power signal is needed to close a contact and become latched. If a mechanically latched vacuum contactor loses control signal, the contacts will stay closed. A separate, short power signal is required to release mechanically latched contacts. This type of contact mechanism will take up slightly more space in the cabinet due to the extra components needed.
Mechanically Interlocked Reverser
To get the most out of your vacuum contactor, you should also consider whether your application requires a mechanically interlocked reverser. Applications that require forward and reverse motion from the motor will most likely need a mechanically interlocked reverser. The mechanically interlocked option offers one contactor dedicated to the forward motion while another is dedicated to reverse direction. You can implement this option by a mechanical “latch” or lever that prevents both contactors from closing at the same time. In this type of application, proper motor function depends on only one contactor operating at a time.
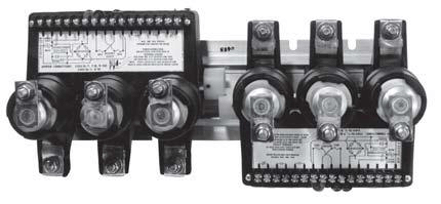